Should you convert your 3d printer to direct-drive or stick with a Bowden system?
Which extruder system is best and does it really matter?
What advantages and disadvantages do the two systems offer?
Direct-Drive & Bowden setups on Ender 3
In order to compare them fairly, both setups use the same components: a BondTech BMG extruder, an E3D V6 hotend, a BLTouch, a 5015 blower fan, and a pancake stepper motor.
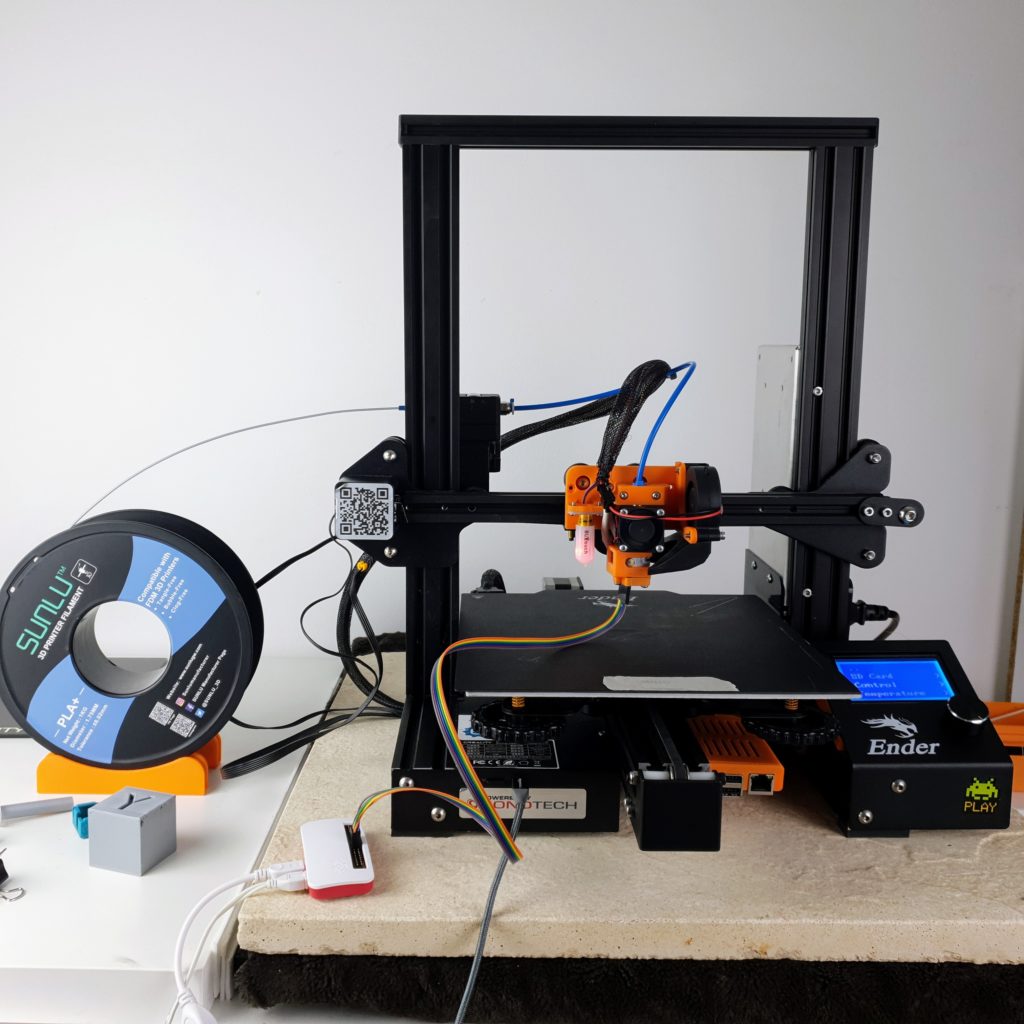
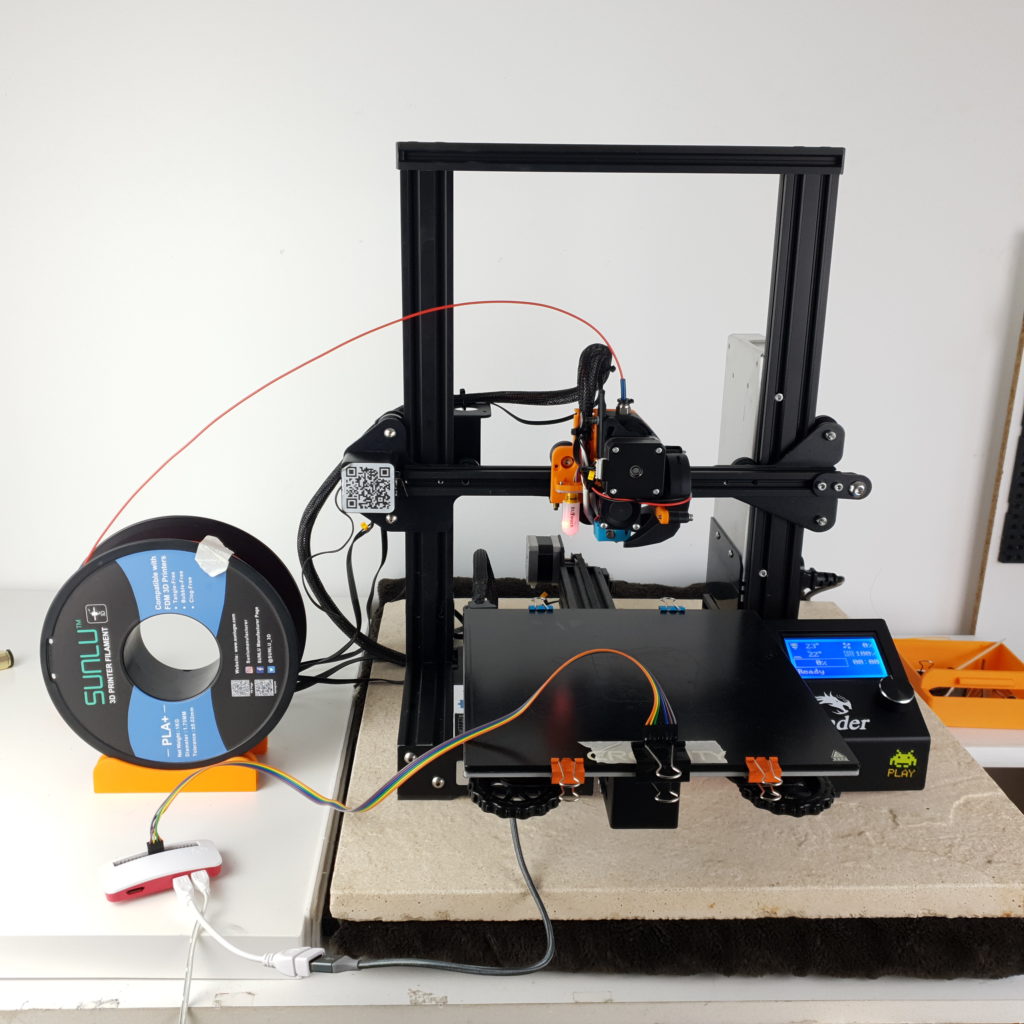
PTFE tube length comparison
In the Bowden system, the extruder is mounted on the printer frame rather than on the printhead. The most obvious difference between the two is the length of the PTFE tube: 350mm long for the Bowden system and only 37mm for the direct-drive!
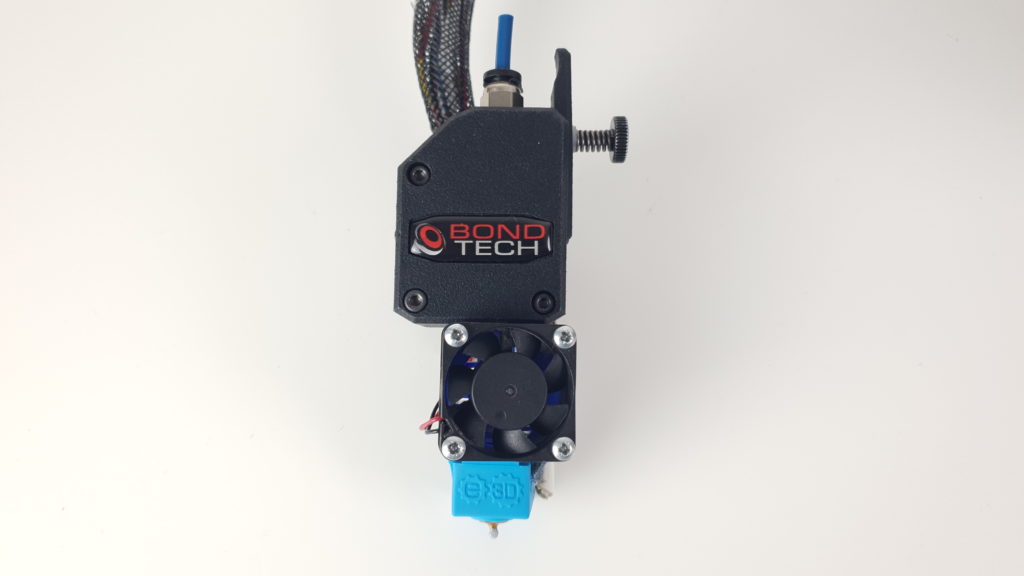
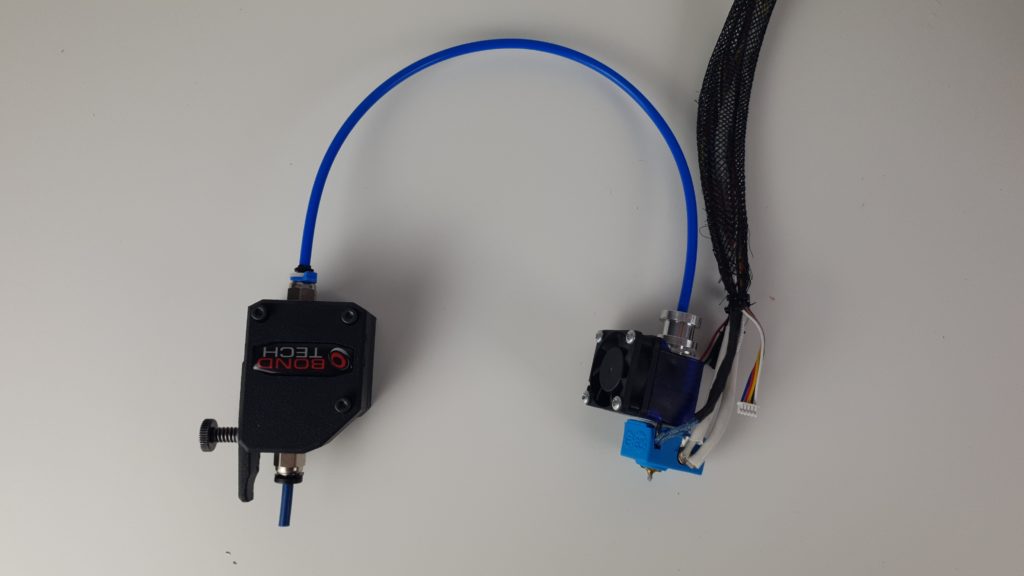
Weight comparison
The Bowden printhead weights only 228 grams. For the direct drive, we add the weight of the stepper motor and the BondTech BMG. This doubles the weight of the printhead. 444 grams.
BOWDEN | DIRECT-DRIVE | |
Carriage with wheels | 87g | 87g |
3d printed adapter | 14g | 14g |
E3D V6 hotend + 30mm fan | 65g | 65g |
BLTouch | 6g | 6g |
5015 part cooling fan | 25g | 25g |
3d printed fan duct | 9g | 9g |
Bolts & Nuts | ~15g | ~15g |
BondTech BMG | 72g | |
Stepper Motor | 138g | |
TOTAL | 228g | 444g |
Less moving weight results in less vibrations and smoother movements. It reduces stress on the printer and the stepper motors.
Print Speed & vibrations
But how does weight impact print quality and speed in practice?
Let’s find out by printing a ringing tower. Surprisingly there is hardly any visible difference in print quality between the 2 parts despite the direct-drive being much heavier, even at high accelerations of 7000mm/s².
Klipper supports Input Shaping, a technique that can dramatically reduce vibrations. Let’s tune input shaping with an accelerometer for both setups and see what we get with input shaping enabled.
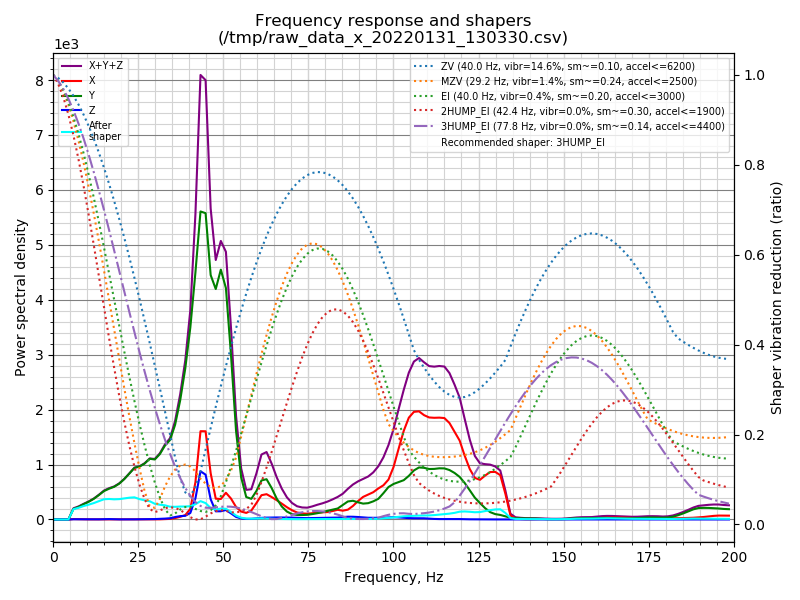
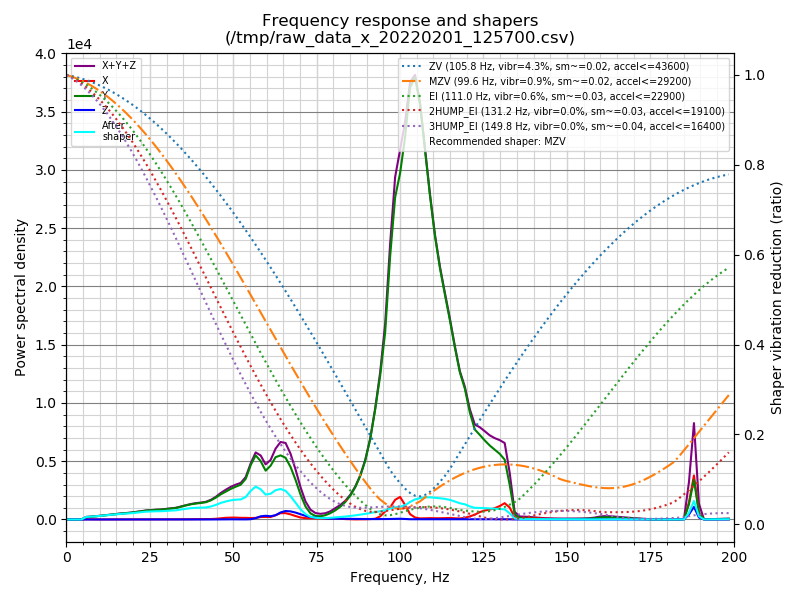
The direct-drive setup has its main resonance frequency at about 42 Hz and the max acceleration is limited to 4400 mm/s². The main resonance frequency of the bowden setup is significantly higher at about 106 Hz. This allows to use a significantly higher acceleration.
BOWDEN | DIRECT-DRIVE | |
Recommended shaper | MZV@99.6Hz | 3HUMP_EI@77.8Hz |
Residual vibrations | 0.9% | 0.0% |
Smoothing | 0.02 | 0.14 |
Max. acceleration | 22900mm/s² | 4400mm/s² |
How does the theory hold up in practice? Let’s print again a ringing tower with both setups, but this time with input shaping enabled.
Input shaping significantly reduces ringing for both setups. But ringing is less visible with the Bowden setup thanks to its lower weight.
Extrusion efficiency
Let’s compare now the extrusion efficiency between the 2 systems.
In the Bowden setup, the extruder motor must push the filament through a much longer tube. This increases the amount of friction and reduces the extrusion force.
In order to quantify the difference between the 2 systems, I extrude 100 mm of filament at various speeds and measure how much filament is actually extruded.
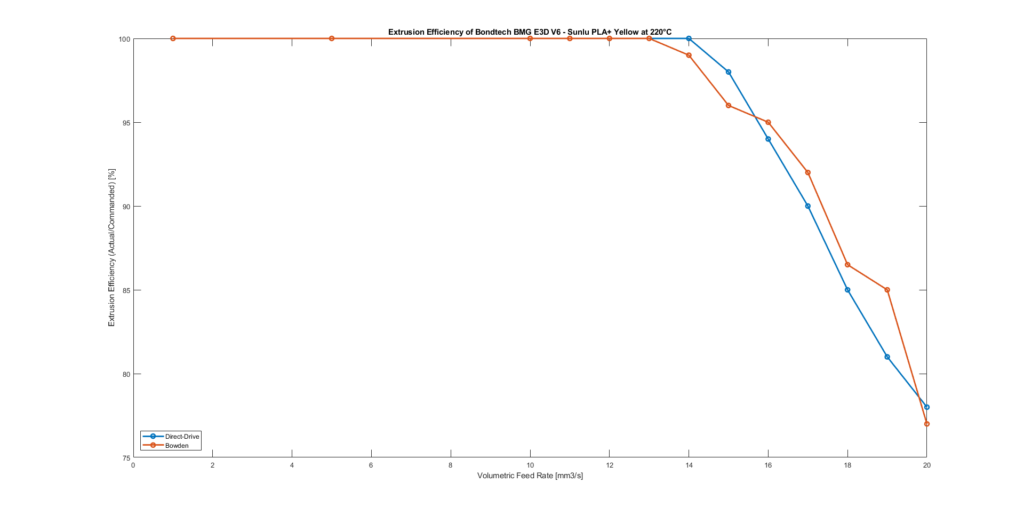
Up to a certain volumetric feed rate, the Bowden system performs almost as well as the Direct-Drive in this test. As long as the extruder as enough torque to overcome the additional friction of the bowden tube, everything is fine.
As the volumetric feed rate increases, the pressure in the nozzle increases.
In the Bowden system, the filament can compress and bend inside the bowden tube which degrades the extrusion.
Retractions
I first print a retraction test with pressure advance disabled. The retraction distance is increased progressively from 0 at the bottom to 5mm at the top.
In direct-drive setups, the distance between the extruder and the hotend is so short that the filament can’t really compress or bend. This results in very responsive and precise retractions. The Direct Drive setup is almost insensitive to the retraction distance. Any value above 0.3 mm provides clean retractions.
The Bowden setup requires very large retraction distances to get rid of stringing, 2 or 3mm. Even when using large retraction distances, the retraction quality is not very good.
In Bowden setups, the long PTFE tube causes too little filament to exit the extruder at the start of extrusion moves and for excess filament to extrude after extrusion ends.
Pressure Advance in Klipper or Linear Advance in Marlin can compensate for this effect. Let’s print a retraction test but with Pressure Advance enabled this time.
The winner for retractions is the Direct-Drive. It is much less sensitive to retraction settings making it easier to calibrate and the retractions are cleaner.
BOWDEN | DIRECT-DRIVE | |
pressure_advance (mm per mm/s) | 0.30 | 0.04 |
pressure_advance_smooth_time (s) | 0.04 | 0.04 |
max_extrude_only_velocity (mm/s) (*) | Default (~80) | Default (~80) |
max_extrude_only_accel (mm/s²) (*) | Default (~800) | Default (~800) |
Min. retraction distance (mm) | >0.8 | >0.3 |
Retraction speed (mm/s) | 80 | 80 |
Best retraction settings for Klipper (**)
(*) Klipper default values for the settings: filament diameter=1.75mm, nozzle diameter=0.4mm, max_velocity=300mm/s and max_accel=3000mm/s²
(**) For Sunlu PLA+ 1.75mm filament, 230°C, 0.4mm nozzle
Filament compatibility
Last but not least, Direct Drive setups are compatible with a wide range of filament. Due to the elastic nature of flexible filaments, they are much easier to print on a Direct-Drive setup.